Even hose that looks clean can have plenty of dirt and contaminants inside.
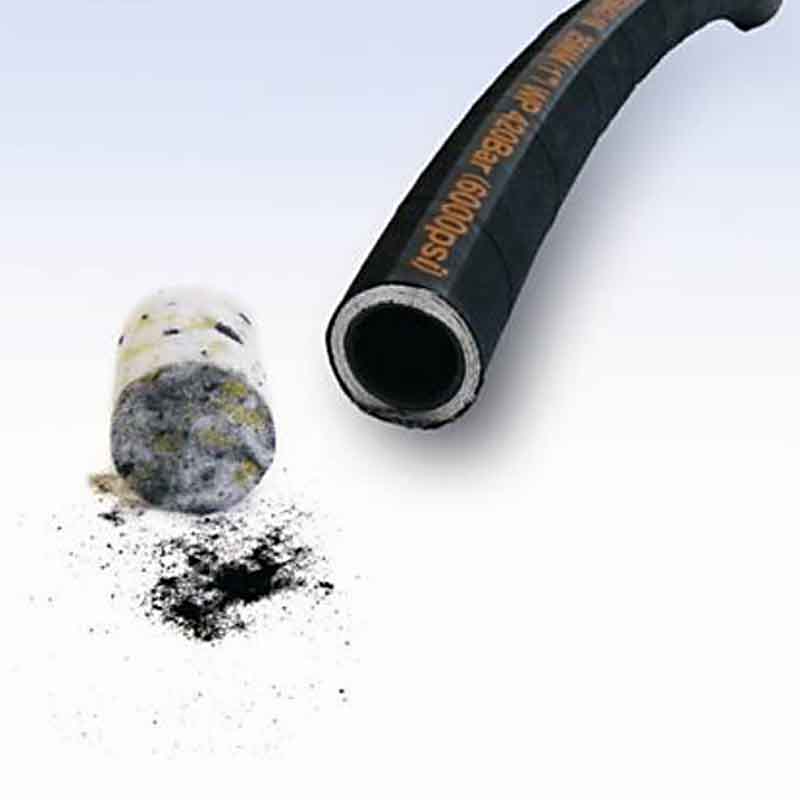
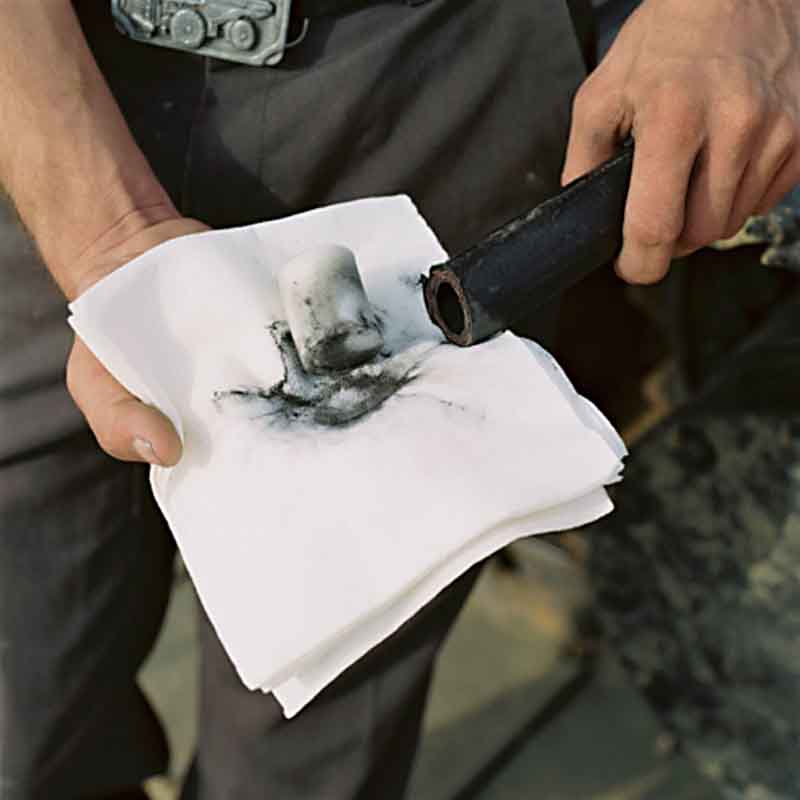
Anyone who works in the hydraulic industry knows the importance of reducing contamination. Particles, dirt, debris and even water that enter a system can quickly wreak havoc, causing system failure and even possibly destroying a component or machine. This is why it is essential to keep these contaminants out.
To ensure hydraulic fluid remains contaminant free, it is imperative to clean all new hoses before installation. If contaminants are left in a hose after it has been shipped to a user or has been cut and crimped, those rubber and dirt particles will easily end up in the reservoir and flow throughout the entire system.
Three common methods are used to remove contaminants from the inner tube of a hydraulic hose: high-pressure air, fluid flushing and projectiles.
1.Air — High-pressure air can be blown through a hydraulic hose or assembly, as long as it is clean and dry. This works best with shorter, smaller hoses, as the longer the hose, the more likely particles may get caught within the assembly.
Shooting foam projectiles through hydraulic hose assemblies ensures dirt and debris is effectively removed. Image courtesy of Ultra Clean Technologies Corp.
2.Fluid flushing — As long as the fluid is clean and compatible with the hose assembly’s inner tube, you can flush an assembly with high-pressure fluids to create turbulent flow. This will remove contaminants from the inner tube wall. However, to ensure the fluid is clean itself, you must use filtration to ensure that the fluid itself is contaminant free. Before you can install the hose, you must ensure that the inside of the hose is then dry.
3.Projectiles — Perhaps one of the most effective methods is through the use foam projectiles that are shot through a hose assembly via dry compressed air or another inert clean gas. Special hand-held or bench-top launchers should be used to ensure the projectile travels completely through the tube and is not left behind inside the hose. The projectiles must be approximately 20 to 30% larger than the ID of the hose tube, as they compress against the wall of the hose assembly to “grab” any dirt and debris.
As the foam projectile travels quickly through the assembly, it picks up any dust, debris and particles and gives the user a visual look at how much contaminants it has removed. It is recommended to use these foam projectiles from both ends of the hose assembly, and then to cap the ends to ensure they remain contaminant free.