ABS is one of the most commonly used material in prototype making,which may take up about 80%.It is a good engineering plastic material and strong enough to meet the requirements of different kinds of prototypes like testing,polishing and painting.It is easy to make it polished by handcrafts.ABS prototypes can be painted and silk-printed as it has good adhesive force.There are many methods to machine ABS prototypes so we need to choose the best way to make our prototypes.
If you need to make a large model with easy structure,then CNC is a good method as it could have high precision of +-0.1mm and don’t need much cost.If your prototype is big and complex,we could make it by CNC separate machining as we could glue the parts together with strongest prototype glue.
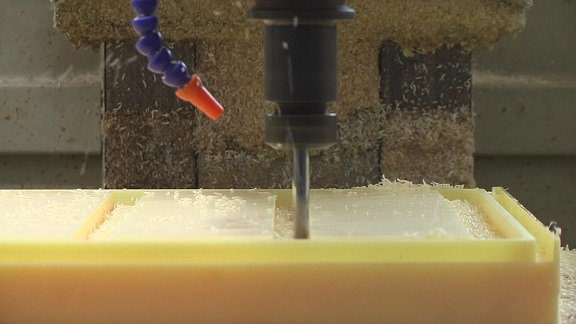
If you need to make a small but complex ABS model,we’d like to advise 3d printing method.The cost is counted on the weight of material it used so it is a cheap and fast method.
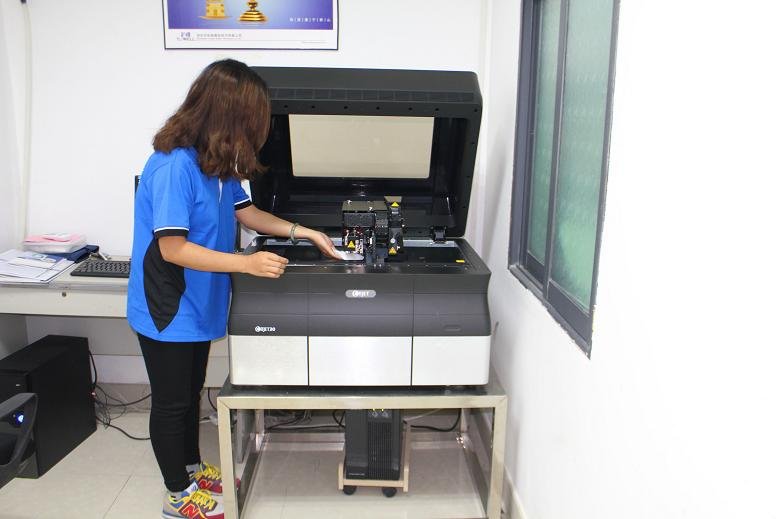
If you need to make low volume ABS prototypes,we’d like to advise vacuum casting process as it is a more economical way than CNC and 3d printing.Here is how it works:firstly we need to make a mother pattern by 3d printing or CNC machining.Then we will make a silicone mold with the pattern.After that we could copy the same parts as the pattern by casting resin.A silicone mold could be used for 10 times.But the disadvantage is the parts made by vacuum casting will be a little deformed and the tolerance will be about +-0.2mm. ?
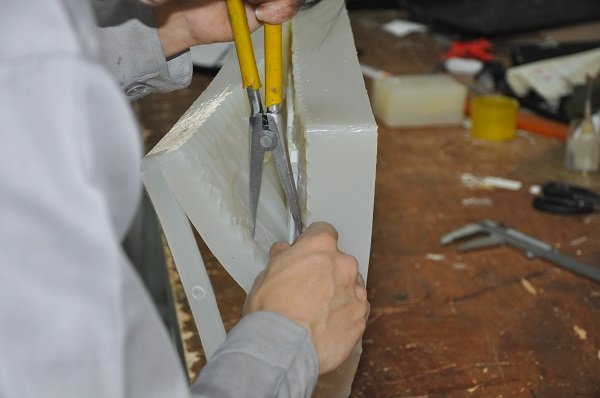
Have you got the points in the article above?If you get it,you could choose the best method to creating your prototypes!