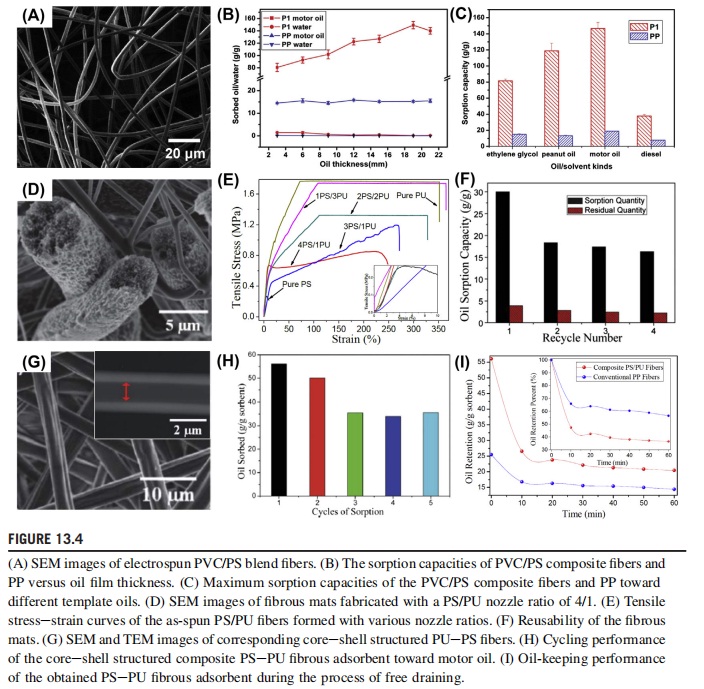
How To Separate Oil From Water By Electrospinning Nanofiber Technology?
1. COMPOSITE POLYMERIC NANOFIBROUS MATS
Due to the relatively weak mechanical strength of PS fibers and the unstable networks of the mats, the practical application performance (e.g., retention over time, oil recovery rate) of pure electrospun PS fibrous absorbents was seriously limited. To overcome this challenging problem, mechanical enhancers with high strength were introduced into the PS fibrous mats to improve their mechanical property. Various criteria must be fulfilled by the reinforcing components: they should be mechanically robust to withstand the tensile or compressive stresses during adsorption and recovery processes of sorbents; and hydrophobic-oleophilic wettability is required to ensure the mats have selective wetting ability. Accordingly, a series of additives such as polyvinyl chloride (PVC), polyurethane (PU), polyvinylidene fluoride (PVDF), and carbon nanotubes (CNTs) were employed to modify the PS fibers via different methods based on electrospinning technology.
To incorporate the reinforcing component into PS fibrous mats, various approaches involving blend electrospinning, multinozzle electrospinning, and coaxial electrospinning have been developed. As shown in Fig. 13.4A-C, PVC/PS composite fibers was first fabricated via directly adding an appropriate amount of PVC to PS solutions, and then made by blend electrospinning. The obtained oil absorbents performed well for motor oil, peanut oil, diesel, and ethylene glycol, with high sorption capacities of 146, 119, 38, and 81 g/g, respectively; these capacities are about five to nine times that of commercial PP melt-blown nonwoven sorbent. The PVC/PS oil adsorbent also possessed excellent oil-water selectivity and good buoyancy, which are important in oil-slick cleanup. Multinozzle electrospinning, a powerful technology in fabricating composite nanofibrous materials, has also been used to make porous PU/PS fibrous mats for oil absorption (Fig. 13.4D-F). The robust elasticity of the PU fibers greatly improves the mechanical strength of the obtained PU/PS fibrous mats, even with low PU contents. As a result the oil absorption performance, especially the reusability of the PU/PS fibrous absorbents, was significantly enhanced. Moreover, core-shell structured fibers were considered as an effective approach to enhance the mechanical property of single fibers. The SEM and the corresponding Transmission Electron Microscopy (TEM) images shown in Fig. 13.4G show that the core-shell structured PU-PS fibers have been prepared with a coaxial electrospinning technique by taking PU and PS solutions as the core and shell, respectively. The obtained PU-PS fibrous sorbent has sorption capacities of 64.40 and 47.48 g/g for motor oil and sunflower seed oil, respectively, which are two to three times that of traditional nonwoven PP fibrous mats with the same template oils (Fig. 13.4H and I). Moreover, the oil adsorption capacity comparable with melt-blown nonwoven sorbent was maintained even after five sorption cycles, giving excellent reusability.
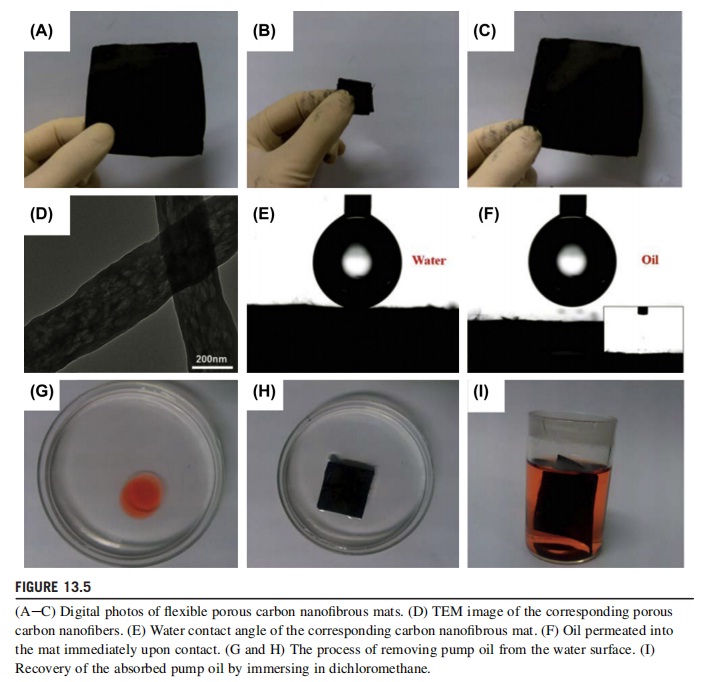
2. CARBON-BASED POROUS NANOFIBROUS MATS
Carbon-based materials have been widely developed to absorb oils due to their instinctive hydrophobic-oleophilic wettability, excellent chemical stability, and thermal stability; this avoids several limitations of organic absorbents, which can be swollen or even dissolved when recycled by rinsing with organic solvents. Recently, electrospun macroporous carbon nanofibrous mats were fabricated through a sublimation method (Fig. 13.5), with terephthalic acid (PTA) used as the pore former to create macropores. During the carbonization of the PTA/polyacrylonitrile (PAN) composite NFs, PTA was sublimed and the macropores were formed, producing flexible and self-sustained macroporous carbon nanofibrous mats. These mats possessed special superhydrophobic and superoleophilic wettability, as well as relatively large porosity of up to 89.2%, attributed to the porous structure of the electrospun fibrous mats. The carbon-based membrane shown a high silicone oil sorption quantity of up to 138.4 g/g, and the absorbed silicone oil could be removed from the membrane by using organic solvents, exhibiting excellent recyclability. Furthermore, a spongelike carbonesilica nanofibrous absorbent with an interconnected three-dimensional structure was also synthesized using the electrospinning technique. The resulting composite fibrous sponge possessed a high porosity of more than 99% and displayed the specific wettability of ultrahydrophobicity and superoleophilicity. With its integral properties of high porosity, low density, and selective wettability, the sponge could adsorb oil up to 140 times of its own weight. Furthermore, oil recovery and sponge regeneration could be easily carried out through circular distilling or mechanical squeezing.
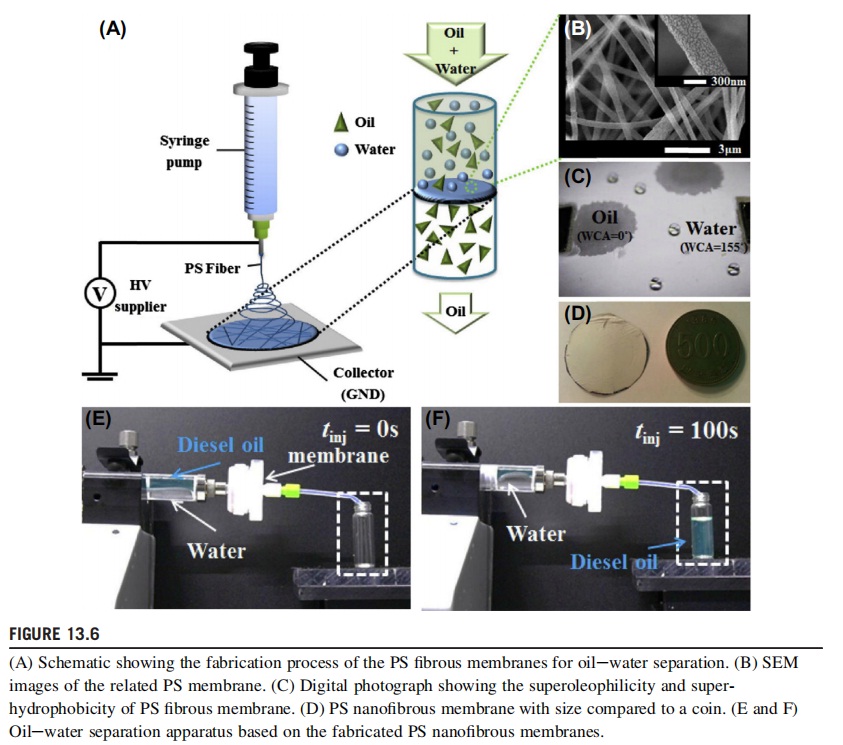
3. ELECTROSPUN NANOFIBROUS FILTER MEMBRANES FOR OIL-WATER SEPARATION
Filtration is another powerful technology for oil-water separation. Unlike the common filtration process for removing solid particulates, achieving efficient separation of oil/water mixtures, especially for emulsions, is quite difficult due to their complex composition, the tiny droplet size in the dispersed phase, and the ease of secondary emulsification. Nowadays, membrane separation technology with the advantages of high separation efficiency and simple operation is considered one of the most promising approaches for the treatment of oily wastewater and purification of oils. For effective separation of oil/water emulsions, a membrane needs to fulfill three criteria: selective wetting ability for the oil or water; appropriate pore size according to the droplet size of emulsions; and high porosity to ensure an acceptable permeation flux under a certain operational pressure. Recently, electrospun nanofibrous separation membranes have attracted considerable attentions with their thinner fiber diameter, high porosity, high surface area, and ease of use.
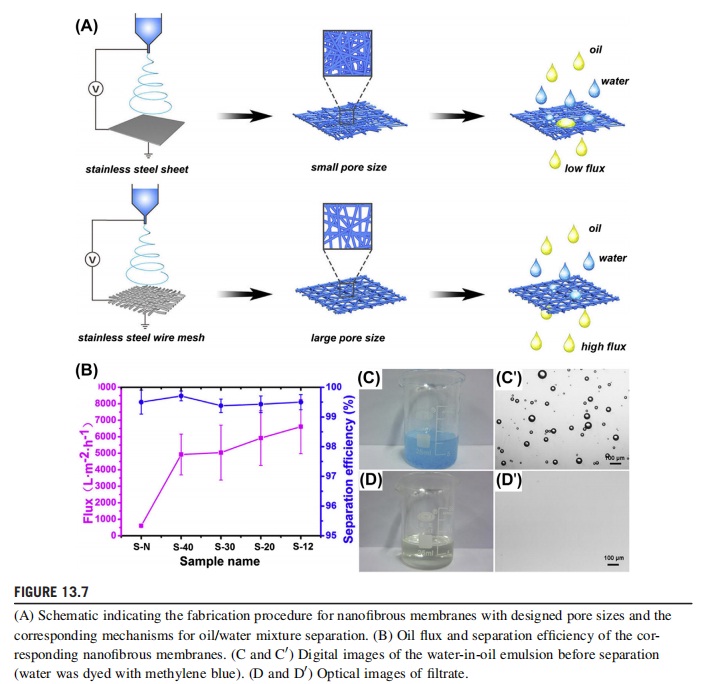
4. HYDROPHOBIC-OLEOPHILIC MEMBRANES FOR OIL-WATER SEPARATION
To separate the water contaminant from oil, an effective and simple method is to use a hydrophobic-oleophilic membrane with appropriate pore size to filter the tiny water droplets while allowing the oil to permeate through (oil-removing type). In general, there are two approaches to fabricate a nanofibrous oil-water separation membrane: one-step electrospinning of the hydrophobic-oleophilic polymers, and incorporation of modification processes.
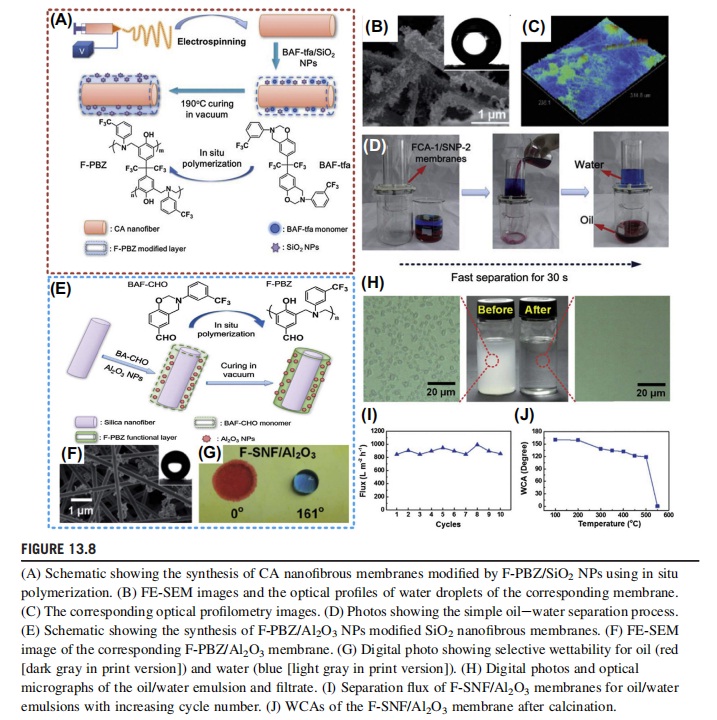
4.1 Instinctive Hydrophobic-Oleophilic Polymeric Membranes
Direct electrospinning of hydrophobic-oleophilic polymers is a simple and effective way to fabricate a filter membrane for oil filtration. As shown in Fig. 13.6, a hydrophobic-superoleophilic membrane was successfully prepared by directly depositing the PS NFs on to a substrate (a stainless steel mesh) via one-step electrospinning. The fabrication process is quite simple, and the raw materials are easy to obtain and inexpensive. With the merits of low free energy of PS and the network-like structures of the membrane, the hydrophobicity of the membranes was significantly enhanced while keeping the intrinsic oleophilic property. As a result, the obtained PS fiber membrane could effectively separate oil/water mixtures in a single step. Other hydrophobic-oleophilic polymers (e.g., PP, PVDF, and PVB) were also directly used to create oil-water separation membranes via one-step electrospinning. For example, a hydrophobic fiber mat made of syndiotactic PP was fabricated for the removing of dispersed water droplets from diesel. Solutions of different weight concentrations of the PP were electrospun to produce submicron-sized fibers of different diameters. These fibrous membranes showed good selective wettability for oil and water, and could effectively remove water from fuel with efficiencies reaching 99%.
Furthermore, electrospun hydrophobic-oleophilic polyvinyl butyral (PVB) NFs were directly deposited on stainless steel wire meshes with different mesh numbers to obtain nanofibrous membranes with different pore sizes (Fig. 13.7). With synergistic effects of selective wettability and tunable porous structure, the obtained PVB nanofibrous membranes had an impressive capability to separate immiscible oil/water mixtures and stable water-in-oil emulsion. In addition, the oil flux of the separation membrane was greatly improved by controlling the pore size, which was about 10 times that of commercial nonwoven filters.
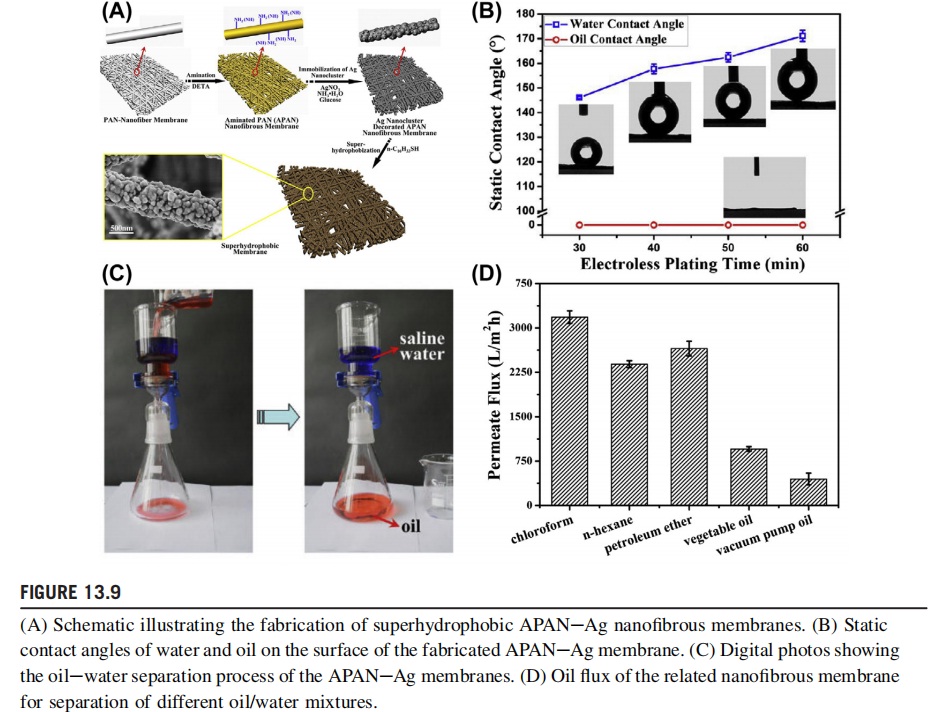
4.2 Modified Superhydrophobic-Oleophilic Composite Membranes
A variety of biomimetic superwettable nanofibrous materials for oil-water separation have been developed based on the synergistic effects of multiscale roughness and low surface energy. According to the principle of the Wenzel and Cassie-Baxter model, the construction of appropriate nano/microscaled roughness can transform a surface from hydrophobic to superhydrophobic, and an oleophilic surface becomes superoleophilic. In general, construction of a multiscale rough surface with low energy requires modifications to the as-spun NFs, including their physical morphology and chemical composition. Based on this theory, a superhydrophobic and superoleophilic nanofibrous membrane was developed using a novel in situ polymerization method to construct a functional layer of silica nanoparticles (SiO2 NPs)/fluorinated polybenzoxazine (F-PBZ) on the surface of electrospun cellulose acetate (CA) NFs (Fig. 13.8A). Benefiting from the low surface energy and excellent oleophilicity of F-PBZ and the hierarchical rough structures, the pristine CA nanofibrous membranes were transformed from instinct hydrophilic to superhydrophobic and superoleophilic, with a water contact angle (WCA) of 161 degrees and oil contact angle (OCA) of 3 degrees. More importantly, the modified nanofibrous membranes were capable of fast, efficient, and stable separation of oil/water mixtures at different pH conditions. Furthermore, the SiO2 NPs/F-PBZ/modified poly(m-phenylene isophthalamide) (PMIA) nanofibrous membrane exhibited promising superhydrophobicity, high thermal stability (350C), and excellent mechanical strength of 40.8 MPa. As a result, the SiO2 NPs/F-PBZ/modified PMIA nanofibrous membranes gave a fast and efficient separation performance for oil/water mixtures. Furthermore, a core/shell structured polyimide/cellulose acetate electrospun fibrous membrane was fabricated by electrospinning and then modified by SiO2 NPs and F-PBZ; the obtained membranes showed much higher critical tensile stress (130 MPa) and superhydrophobic-superoleophilic wettability, and could effectively separate various oil/water mixtures solely driven by gravity, with high flux (3106.2 100 L/m2 h) and high separation efficiency (>99%). As shown in Fig. 13.8B, ceramic nanofibrous membranes, such as the F-PBZ/Aluminium oxide nanoparticles (Al2O3 NPs) modified SiO2 nanofibrous membranes, were also fabricated by the in situ polymerization method, and the obtained membranes gave effective gravity-driven separation performance for water-in-oil emulsions with a relative high flux of 892 L/m2 h, and had good antifouling property, thermal stability, and durability. Apart from in situ polymerization of F-PBZ, other chemicals (e.g., Nafion, beeswax, and n-hexadecyl mercaptan) have successfully been employed to create superhydrophobic and superoleophilic nanofibrous membranes for effective oil-water separation. As shown in Fig. 13.9, a uniform and hierarchical rough layer can be constructed on the surface of single electrospun NF via a simple combination of the amination of PAN NFs (APAN) and immobilization of Ag nanoclusters on the surface of fibers (APAN-Ag) using an electroless plating technique. This APAN-Ag nanofibrous membrane was modified with alkyl thiols: the modified nanofibrous membrane was superhydrophobic and superoleophilic, and had an excellent capability for oil-water separation in a hypersaline environment and a broad range of pH conditions.
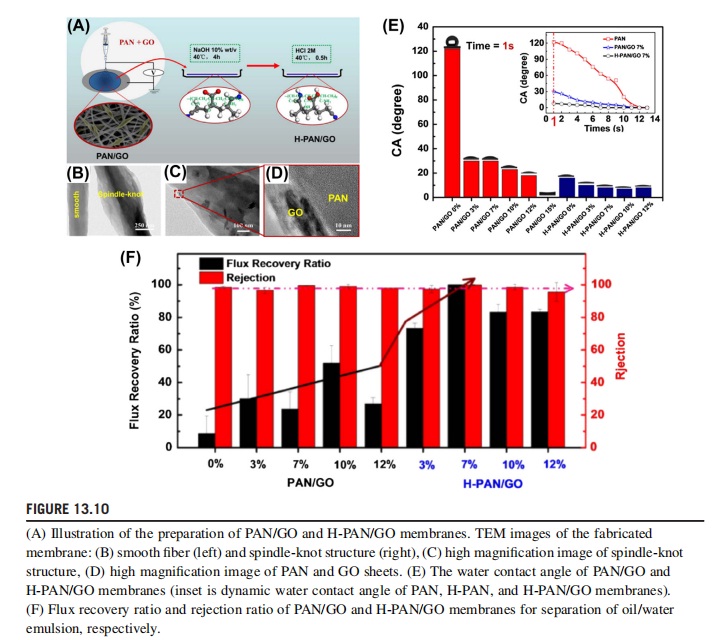
5. HYDROPHILIC-OLEOPHOBIC MEMBRANES FOR OIL-WATER SEPARATION
Membrane separation is the most promising technology to treat oily wastewater, and ultrafiltration and nanofiltration membranes have been used in many industrial oil-water separation processes. Conventional ultrafiltration and nanofiltration membranes have fairly high separation efficiency for oil/water emulsions, but suffer from low flux, which is attributed to their limited permeability and serious surface fouling. To overcome these problems two aspects should be considered: constructing a hydrophilic surface to avoid oil fouling of the membranes, and increasing the porosity and decreasing the thickness of the separation layer.
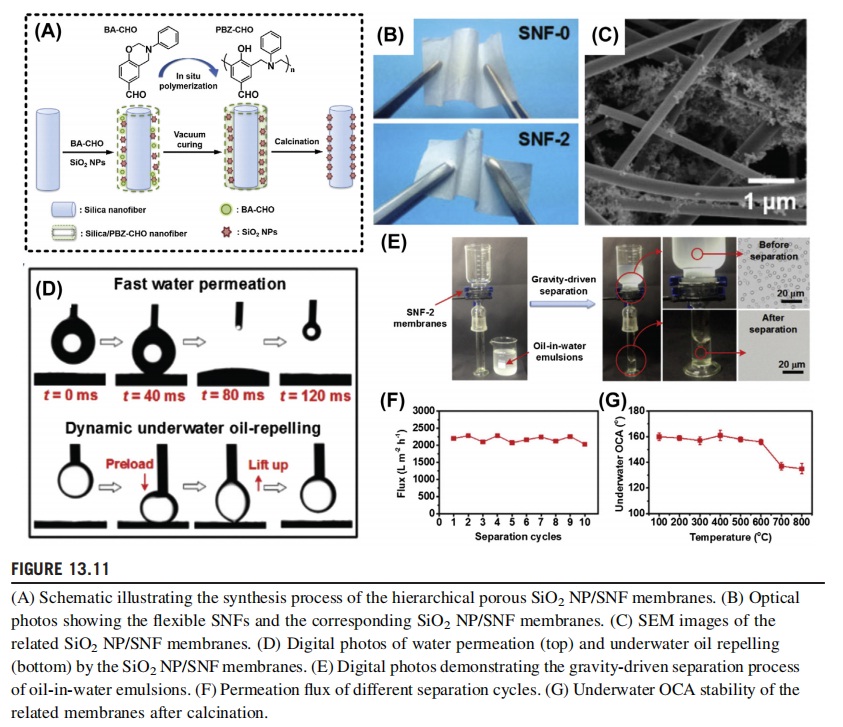
5.1 Single-Layer Superhydrophilic-Oleophobic Nanofibrous Membranes
Inspired by the oil-repellent abilities of creatures in nature (such as fish scales), a superhydrophilic and underwater superoleophobic surface could be constructed by combining a hydrophilic chemical surface and appropriate roughness into polylactide NFs using the blending electrospinning method. The obtained composite nanofibrous membrane had good hydrophilicity and high water permeability, endowing it with the superior separation performance of oil-in-water emulsion under gravity. Besides blending electrospinning, dip coating is also an effect approach to modify nanofibrous membranes. Ahmed et al. employed cellulose regenerated from its ionic liquid solution to coat electrospun PVDF-co-hexafluoropropylene (PVDF-HFP). After modification with cellulose, the membrane had smaller pores with narrower pore size distribution: it exhibited superhydrophilicity and underwater superoleophobicity, and was successfully used for oil-water separation with quite high efficiency. Recently, a composite membrane made from graphene oxide coating aminated polyacrylonitrile (GO/APAN) fibers was fabricated by controlled assembly of GO sheets on the surface of electrospun APAN fibers and in the gaps between fibers. This membrane was superhydrophilic, had low oil adhesion, and exhibited ultrahigh flux, a preferable rejection ratio, and remarkable antifouling performance for the separation of oil/water emulsions. Furthermore, as shown in Fig. 13.10, a PAN/GO composite fibrous membrane with spindle-knot structured NFs was fabricated by electrospinning and then hydrolyzed (H-PAN/GO) to tailor its chemical features. With the combination of chemical features of hydrolyzed PAN and a spindle-knotted structure, the antifouling performance of the composite membrane was enhanced and it performed well in separating oil/water emulsions.
Compared to polymers, ceramic nanofibrous membranes have potential advantages in terms of relatively high surface energy, relatively stable chemical properties, and good antifouling ability. As shown in Fig. 13.11, Yang et al. used electrospun SiO2 NFs (SNFs) as the template, and anchored the SiO2 NPs uniformly on the surface of SNFs through a novel in situ synthesis method to fabricate flexible, thermally stable, and hierarchically porous structured composite membranes with highly selective wettability of superhydrophilicity and underwater superoleophobicity. With prominent selective wettability and high porosity, the obtained SiO2 NP/SNF composite membranes exhibited an extremely high separation flux up to 2237 L/m2h and high separation efficiency for a surfactantstabilized oil-in-water emulsion. In further studies, NiFe2O4 NPs were incorporated in SNFs to fabricate hierarchical magnetic nanofibrous membranes: these membranes were able to separate surfactant-stabilized oil-in-water emulsions effectively in a relatively high separation flux.
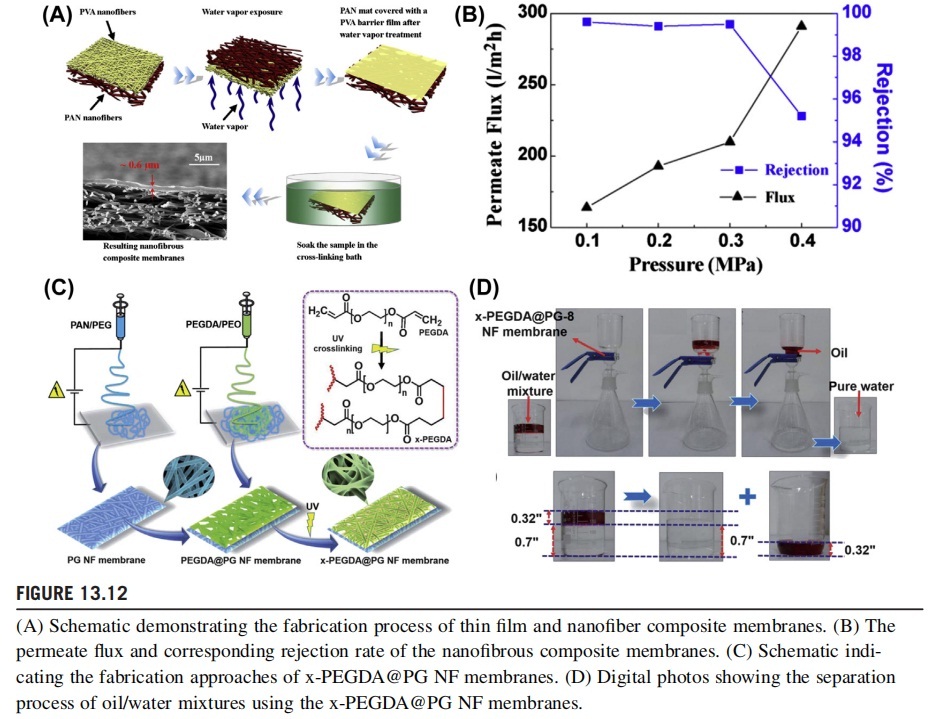
5.2 Multilayer Structured Superhydrophilic-Oleophobic Nanofibrous Membranes
Constructing a separation layer with high selective wettability and small pore size on the surface of electrospun nanofibrous membranes is an effective way to enhance oil-water separation efficiency. Various composite nanofibrous membranes have been developed for high flux and high efficiency separation of oil-in-water emulsions. The main idea is to deposit a very thin hydrophilic polymeric layer of poly(vinylalcohol) (PVA), chitosan, polyamide, or even ultrafine polysaccharide NFs on to electrospun nanofibrous membranes via physical absorption or interfacial polymerization. As shown in Fig. 13.12, a double-layer separation membrane was fabricated by depositing the PVA NFs on electrospun PAN nanofibrous membranes, and then remelting and cross-linking the PVA nanofibrous layer to construct a nonporous PVA film with a thickness of several micrometers. Using this hydrophilic PVA layer, the composite membrane could effectively separate oil-in-water emulsions with excellent antifouling properties. In general, when a microporous or nonporous coating layer is constructed on the surface of a nanofibrous membrane, the water-permeate flux of the obtained composite membrane will be significantly reduced, which is attributed to the hydraulic resistance of the coating layer. To address this problem, Raza et al. fabricated superhydrophilic and oleophobic nanofibrous membranes by incorporating a composite layer of polyethylene glycol (PEG) diacrylate NFs on PAN/PEG nanofibrous membranes (x-PEGDA@PG NF) using the in situ cross-linked method. The obtained x-PEGDA@PG NF membranes could be completely wetted by water within a very short time and the superhydrophilic layer could trap a layer of water on the surface of membrane; this blocked the contact of oil with the membrane, thus making the membrane oleophobic. Benefiting from the high selective wettability and high porous structures, the membranes were capable of effectively separating immiscible oil/water mixtures and oil-in-water emulsions with high capacity and robust antifouling property. Most recently, a novel superhydrophilic and underwater superoleophobic nanofibrous membrane with a hierarchical structured skin for the separation of oil-in-water emulsions was prepared via electrospinning and electrospraying methods. Unlike the conventional nonporous polymeric film or submicro fibrous layer, the hierarchical structured SiO2/PAN microspheres bonded with monofilament significantly enhanced the wetting selectivity and antifouling properties of the composite membranes. With the combination of a superwettable hierarchical structured skin layer and a high-porosity nanofibrous substrate, the membranes performed well in separating microscaled oil-in-water emulsions solely under the driving force of gravity with excellent separation efficiency and high fluxes.