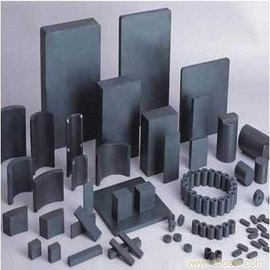
Permanent ferrite magnets are the basic functional materials in the electronic industry.
Permanent magnet materials, as an important part of magnetic materials, play an important role in the electronics industry, information industry, motorcycle, power tools industry, automobile industry and other industries.Permanent magnet ferrite material is a functional material that generates magnetic field.
Permanent magnet ferrite is made from SrO or BaO and ferric oxide through ceramic process. There are 9 kinds and bonded (plastic magnetic) permanent magnet ferrite such as DM10T, DM20, DM25, DM30, DM33H, DM34H, DM42B, DM43 and DM43B produced by permanent magnet product company.
Due to its low raw material price and relatively simple production process, the finished product price is relatively lower than other magnets.
The main raw material of ferrite magnet is oxide, so it is not affected by the environment or chemical substances (except strong acid) and corrosion, so the surface does not need electroplating treatment.
Ferrite magnet product is mainly used in crafts, adsorbents, toys, motors, loudspeakers, etc.
What should be paid attention to during the production of permanent magnet ferrite components? On the below are from Zhongke magnet:
Ferrite magnet is a permanent magnet. It can be a natural product, also known as pump magnetic natural magnet, or it can be manufactured by permanent magnet ferrite (the strongest magnet is Ndfeb magnet). It has wide hysteresis loop, high coeruleity and high remanence, also known as permanent magnetic materials, hard magnetic materials.
In application, permanent magnet operates in the second quadrant of the demagnetization portion of the depth magnetic saturation and magnetization magnetic rayback line.
Permanent magnets should have a coerciousness Hc, remanence Br and maximum magnetic energy (BH) m with the highest possible radial magnetic force, so as to ensure maximum magnetic energy storage and stable magnetism.
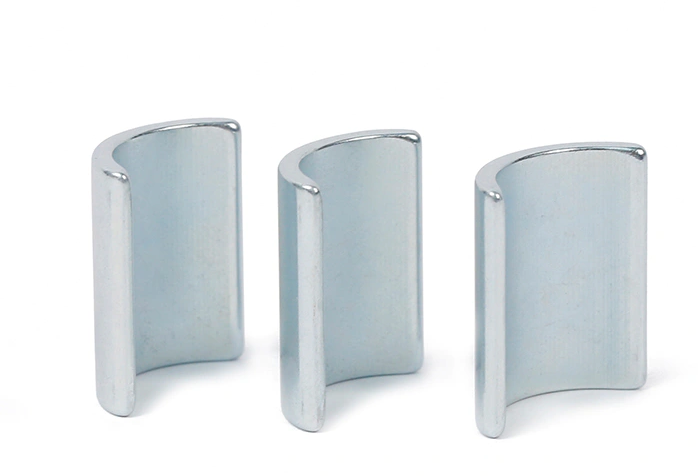
At present, the dry production method is used to prepare permanent magnet ferrite prefiring materials. The traditional method has the following disadvantages:
I. When ball mill of production line carries out ball mill, water pump magnetism cannot be continuously produced, so intermittent radial rotor can only be produced in batches. In the process of production, the powder which is ground to meet the requirements cannot be discharged in time.
2. Abrasive time is longer, the production of permanent magnet ferrite is low efficiency, which could affect the production efficiency of the whole production line for permanent ferrite magnet.
3. The poor particle size uniformity of the ground iron and phosphorus powder seriously affects the chemical reaction degree of strontium carbonate additives, thus affecting the performance and stability of magnetic material finished products.
4. Uneven mixing results in low grade, unstable quality and poor efficiency.
A new device and a new method for preparation of permanent ferrite magnet prefiring materials have been successfully developed in China. The raw materials produced by permanent magnet ferrite prefiring materials have small particle size distribution, uniform mixing, high grade, stable quality, large batch, high production efficiency and low labor intensity.
New technology is a method of preparation of permanent magnetic ferrite pre under-burnt clinker dry, its process flow, raw material (iron phosphorus) cleaning a drying a ball mill, sizing ingredients (iron phosphate, iron oxide red, strontium carbonate, additives) a strong mixing feeding a pelletizing, conveyor belt, presintering rotary kiln firing a cooling water system, ball mill grinding ball grading inspection.
The method of new technology provides a continuous production process and device with higher precision and lower energy consumption in product production.
New technology of preparation of permanent ferrite magnetic pre under-burnt clinker dry device is characterized in addition to the ball mill group, the mix of bin, dry preparation of permanent magnetic ferrite devices, in the process of under-burnt clinker crushing iron scale ball mill of permanent magnetic ferrite under-burnt clinker beforehand I and smash the ball mill II are connected to the classifier, which can pass the classifier classification quickly, not only can reduce the time of ball mill and greatly save energy consumption.
The new technology is equipped with a grader, and the ball mill grinded powder is detected and separated by the grader, and the qualified raw material is sent to the mixing bin by airflow, and the unqualified raw material is adjusted and ground, and repeated cycles are carried out until the particle size and moisture are qualified and then sent to the mixing bin.
This greatly saves abrasive time and reduces energy consumption for permanent ferrite magnet product; The uniformity and consistency of iron scale powder were greatly improved to large batch, high efficiency, significant economic benefits for permanent ferrite magnet.