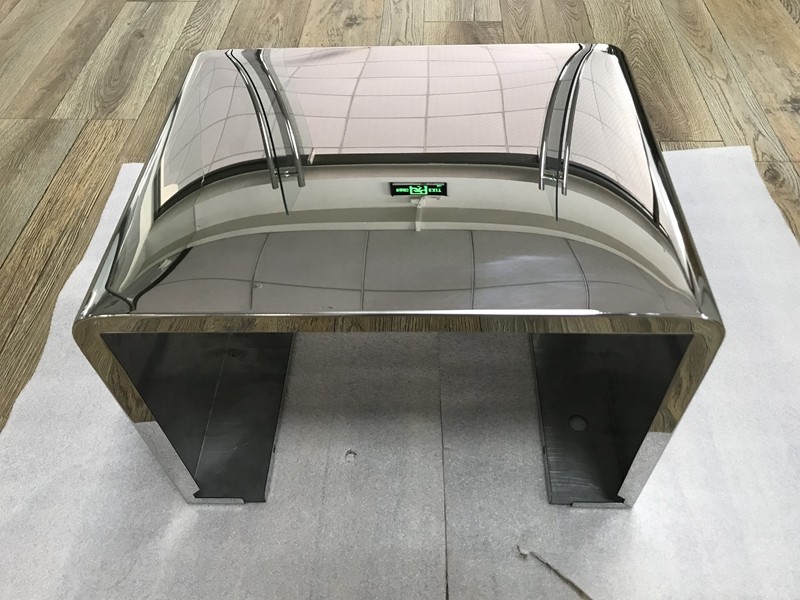
Polishing does not improve the dimensional accuracy or geometric accuracy of the workpiece, but rather for the purpose of obtaining a smooth surface or specular gloss, and sometimes for eliminating gloss (extinction). A polishing wheel is usually used as a polishing tool. The polishing wheel is generally formed by stacking a plurality of layers of canvas, felt or leather, and the two sides are clamped by a metal circular plate, and the rim is coated with a polishing agent uniformly mixed with fine powder abrasive and grease.
During polishing, the high-speed rotating polishing wheel (circumferential speed of 20 m / sec or more) is pressed against the workpiece, causing the abrasive to roll and micro-cut on the surface of the workpiece, thereby obtaining a bright machined surface with a surface roughness of Ra0.63. ~0.01 microns; when a non-greasy matting finish is used, the shiny surface can be matted to improve appearance. When mass producing bearing steel balls, the method of barrel polishing is often used.
In the rough polishing, a large number of steel balls, lime and abrasive are placed in the inclined can-shaped drum. When the drum rotates, the steel ball and the abrasive are randomly rolled and collided in the cylinder to remove the surface convex surface and reduce the surface roughness. The purpose is to remove the margin of about 0.01 mm.
In the case of fine polishing, steel balls and fur fragments are placed in the wooden barrel, and the surface is rotated for several hours to obtain a dazzling and bright surface. The polishing of the precision ruler is carried out by immersing the processed surface in a polishing liquid, and the polishing liquid is prepared by mixing chrome oxide fine powder having a particle size of W5 to W0.5 and an emulsion. The polishing wheel is made of finely degreased wood or special fine felt. The movement track is a uniform dense mesh. The surface roughness after polishing is not more than Ra 0.01 μm. Observed under a microscope magnified 40 times. Not any surface defects. In addition, there are methods such as electrolytic polishing.
Chemical polishing:
Chemical polishing is the smoothing of the metal surface by regular dissolution. In the chemical polishing process, the surface of the steel parts is continuously formed with a passivation oxide film and the oxide film is continuously dissolved, and the former is stronger than the latter. Due to the microscopic inconsistency of the surface of the part, the microscopic convex part of the surface is preferentially dissolved, and the dissolution rate is greater than the dissolution rate of the concave part; and the dissolution of the film and the formation of the film are always performed simultaneously, but the rate is different, resulting in the surface of the steel part. The roughness is leveled to obtain a smooth, shiny surface. Polishing can fill surface pores, scratches and other surface defects, thereby increasing fatigue resistance and corrosion resistance.
Process flow:
Chemical (or electrochemical) degreasing → hot water washing → flowing water washing → descaling (10% sulfuric acid) → flowing water washing → chemical polishing → flowing water washing → neutralization → flowing water washing → transfer to the next surface treatment process
Working environment: The traditional polishing process has a harsh working environment, and sand, iron filings, dust, etc. are generated during the polishing process, which seriously pollutes the environment;
Processing efficiency: manual polishing; Hawker energy process belongs to the car grinding, the line speed can reach 50-80 m/min, the feed rate can reach 0.2-0.5mm/r, which is equivalent to the efficiency of semi-finished car.
Paving consumption: polishing requires the consumption of polishing wheels, abrasives, abrasive belts and other accessories;
Adaptability: Polishing can process simple profiles such as planes, and can not be processed for curved surfaces. If you are processing complex surfaces such as R arcs and curved surfaces, you can use the Hawker polish process.
Post processing:
Chemical polishing of steel parts can be used as a pre-treatment process for protective decorative plating, or as a pre-treatment process for chemical film formation such as phosphating. If it is not applied by electroplating or chemical film formation, it can be sprayed with amino varnish or acrylic varnish, which has good protective decorative effect after drying. If the rust-proof passivation solution is immersed before painting, the corrosion resistance will be further improved.
How to polish?
1. Mechanical polishing Mechanical polishing is a polishing method that removes the polished convex portion by plastic deformation on the surface of the material to obtain a smooth surface. Generally, oil stone strips, wool wheels, sandpaper, etc. are used, mainly by manual operation, and special parts such as rotation For the surface of the body, an auxiliary tool such as a turntable can be used, and the method of super-fine polishing can be used for the surface quality. Ultra-fine grinding and polishing is a special-purpose grinding tool. In the polishing liquid containing abrasive, it is pressed against the machined surface to perform high-speed rotary motion. With this technology, a surface roughness of Ra0.008 μm can be achieved, which is the highest among various polishing methods. This method is often used in optical lens molds.
2. Chemical polishing Chemical polishing is the process in which the material is slightly fused in the chemical medium, and the concave portion is preferentially dissolved to obtain a smooth surface. The main advantage of this method is that it can polish a workpiece with complex shapes without complicated equipment, and can polish many workpieces at the same time with high efficiency. The core issue of chemical polishing is the formulation of the polishing fluid. The surface roughness obtained by chemical polishing is generally several 10 μm.
3. Electropolishing The basic principle of electropolishing is the same as chemical polishing, which is to selectively dissolve the surface of the material to make the surface smooth. Compared with chemical polishing, the effect of the cathode reaction can be eliminated, and the effect is good. The electrochemical polishing process is divided into two steps: (1) Macro-leveling The dissolved product diffuses into the electrolyte, and the surface roughness of the material decreases, Ra>1 μm. (2) Low-light leveling Anodic polarization, surface brightness is improved, Ra<1μm.
4. Ultrasonic polishing The workpiece is placed in the abrasive suspension and placed together in the ultrasonic field. The abrasive is ground and polished on the surface of the workpiece by the vibration of the ultrasonic wave. Ultrasonic machining has a small macroscopic force and does not cause deformation of the workpiece, but it is difficult to manufacture and install the tooling. Ultrasonic processing can be combined with chemical or electrochemical methods. On the basis of solution corrosion and electrolysis, the ultrasonic vibration stirring solution is applied to dissociate the dissolved products on the surface of the workpiece, and the corrosion or electrolyte near the surface is uniform; the cavitation of the ultrasonic wave in the liquid can also inhibit the corrosion process, which is favorable for surface illuminating.
5. Fluid polishing is performed by polishing the surface of the workpiece with the high-speed flowing liquid and the abrasive particles it carries. Common methods are: abrasive jet processing, liquid jet processing, hydrodynamic grinding, and the like. The hydrodynamic grinding is hydraulically driven to cause the liquid medium carrying the abrasive particles to flow back and forth across the surface of the workpiece at high speed. The medium is mainly made of a special compound which flows at a lower pressure and is doped with an abrasive, and the abrasive can be made of silicon carbide powder.
6. Grinding and polishing Magnetic grinding and polishing is the use of magnetic abrasive to form an abrasive brush under the action of a magnetic field to grind the workpiece. This method has high processing efficiency, good quality, easy control of processing conditions and good working conditions. With a suitable abrasive, the surface roughness can reach Ra 0.1 μm.
Mainstream technology:
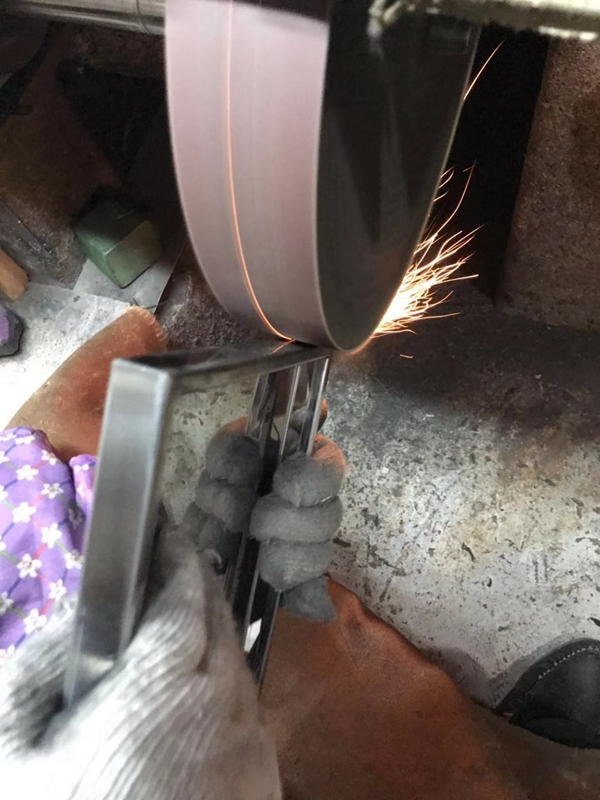
2. Physical + cover grinding
The scratches that have just been thrown out disappear, and there is a bright effect, but there are obvious slight scratches and optical rotation under the sunlight. The reason: some scratches are filled with wax or resin oily ingredients, not really removed; oily, too large, Polished hair ball walking lines produce optical rotation. This kind of polishing method is easy to reproduce after scratching two or three cars, and it is highly deceptive. I don't know why the owner and technician will be very upset!
3. Compare top and rare grinding technology
Time-lapse crushing and polishing technology, the abrasive is round in the shape of beads, which will not cause secondary grinding scratches, and the temperature of the paint surface is low; when the polishing ball is running at a high speed and the abrasive generates a certain temperature, the abrasive particles are instantaneously Broken, forming finer particles, effective for fine deep polishing, one step in place, the more polished, the polishing technology guarantees the effect, and also minimizes the damage of the polishing to the paint surface (polishing must hurt)! This kind of abrasive does not contain wax or resin oily ingredients, and the luster that is thrown is the lacquer gloss of the lacquer surface. The cold light texture is amazing today.