Firstly use software to build a model, and then split the 3D model to a layer-by-layer cross-section, ie, slicing, so as to guide the printer to print layer by layer.
The standard file format between design software and printers is the STL file. A STL file uses a triangular face to approximate the surface of a simulated object. The smaller the triangular face, the higher the generated surface resolution. PLY is a scanner that generates a 3D file by scanning, and the generated VRML or WRL file is often used as an input file for full-color printing.
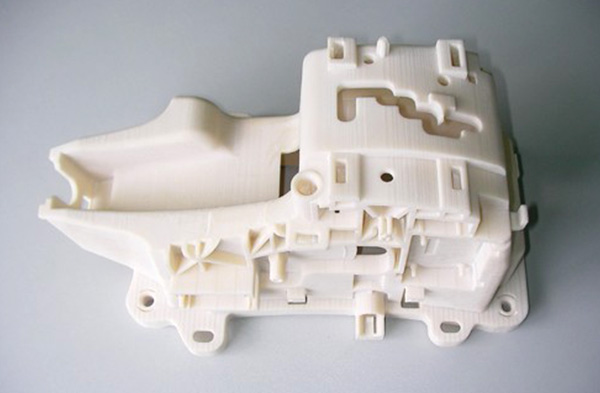
The processing process is to use a powder spreading stick to lay a layer of powder material on the upper surface of the formed part and heat it to a temperature just below the sintering point of the powder, and the control system controls the laser beam according to the cross-sectional profile of the layer in the powder. The upper scan causes the temperature of the powder to rise to the melting point, is sintered, and is bonded to the formed portion below. When the sintering of one layer is completed, the workbench is lowered by the thickness of one layer, and the paving roll is coated with a layer of evenly dense powder to perform sintering of a new layer until the entire model is completed.
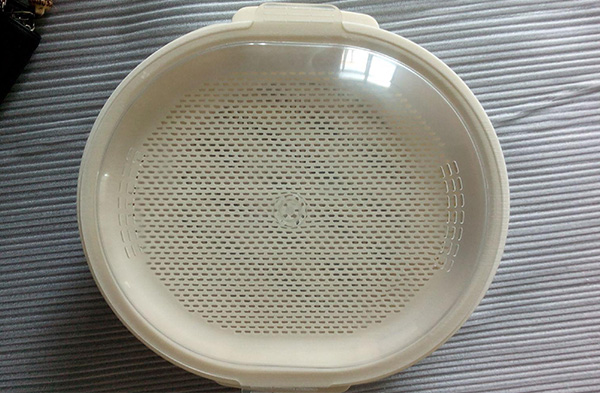
The laser used in SLS is a carbon dioxide laser. The raw materials used are wax, polycarbonate, nylon, slender nylon, synthetic nylon, metal and some developing materials.
The Advantages of SLS Rapid Prototyping
In principle, this method can be applied to any powder material with reduced viscosity when heated, and can be made into any shape by materials or various types of binder-containing coating particles to meet different needs.
Due to the variety of materials available, the selective laser sintering process can directly produce complex shaped prototypes, cavity mold 3D components or components and tools, depending on the materials used.
Depending on the type and particle size of the material used, the geometry and complexity of the product, the process typically achieves a tolerance of ±(0.05--2.5) mm over the entire range of the workpiece. When the particle size of the powder is 0.1 mm or less, the prototype accuracy after molding can reach ±1%.
Since the process does not require a support structure, does not have a lot of waste as in the LOM process, and does not require substrate support, the process is the highest in many common rapid prototyping processes and can be considered as 100%. Most of the powders used in the SLS process are less expensive, so the cost of the SLS model is also lower.
From CAD design to the completion of parts processing, it takes only a few hours to tens of hours. The entire production process is digitized and can be modified at any time and manufactured at any time. This feature makes it particularly suitable for the development of new products.
it can realize functions such as rapid casting, rapid mold manufacturing, and small batch parts output, and inject new vitality into traditional manufacturing methods.
Due to the variety of molding materials, the SLS process is suitable for a variety of applications, such as prototype design verification, mold master, precision casting, casting shells and cores.